In the busy petrochemical industry, focusing on efficiency, safety, and following rules is very important. One important tool that helps achieve these goals is the RF3700 Rocksensor thermal mass flow meter.
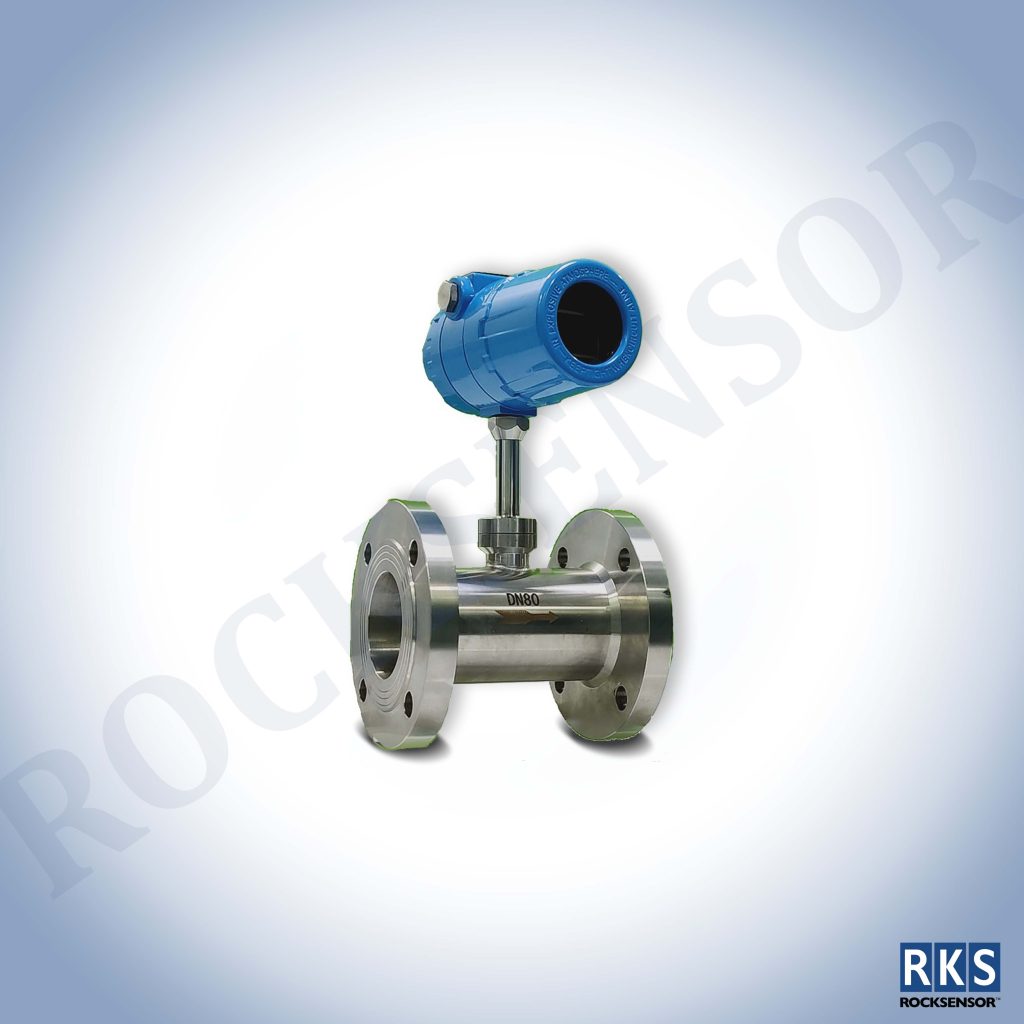
Introduction
The RF3700 Rocksensor Thermal Gas Mass Flow meter is designed based on the principle of thermal dispersion which uses the constant temperature difference method to accurately measure gas mass flow rate. It has advantages of small size, easy installation, high reliability and high accuracy, etc. The sensor part consists of two reference grade platinum resistance temperature sensors. When the instrument is working, one of the sensors is a Temperature sensor which continuously measures the medium (Gas) temperature ‘T1’, while the other sensor is a heater which is maintained at temperature ‘T2’ such that a constant differential temperature ‘T2-T1’ temperature is maintained. The temperature ΔT = T2 — T1, T2>T1, when the fluid is flowing, the gas molecules collide with the heater sensor and take away the heat of T2, so that the temperature of T2 is lowered. To keep ΔT unchanged, it is necessary to increase ‘T2’. The greater the gas velocity, the greater the cooling effect and power required to maintain the differential temperature. The measurement of heater power is therefore a measurement of the gas mass flow rate
m = Kq/(Cp(T2 — T1))
The mass flow (m) is calculated on the basis of the measured temperature difference (T2 — T1), the meter coefficient (K), the electric heat rate (q), and the
specific heat of the fluid (Cp).
Let’s dive into the various applications of these innovative devices, particularly in flare gas systems.
Flare Gas Emission Monitoring
In the quest for environmental compliance, petrochemical plants rely on thermal mass flowmeters to monitor flare gas emissions. These meters meticulously track the amount of gas being flared, ensuring that facilities meet stringent environmental regulations, such as the guidelines set forth by the EPA(Environmental Protection Agency). Furthermore, by providing precise calculations of greenhouse gas emissions — like CO₂ and methane — these meters assist in accurate carbon emission reporting, helping companies uphold their environmental responsibilities.
Mass Flow Measurement
One of the standout features of thermal mass flowmeters is their ability to measure mass flow directly. In flare gas systems, where flow conditions can fluctuate dramatically, this accuracy is indispensable. These meters excel in low flow sensitivity, allowing them to measure even the faintest flows in large pipes. This capability is particularly beneficial in flare gas applications, where gas flow may be intermittent or exceptionally low.
Leak Detection and Maintenance
Safety is always a priority in petrochemical operations, and thermal mass flowmeters contribute significantly to this aspect. They can identify fugitive emissions, alerting operators to unexpected gas leaks or minor emissions within the flare system. With continuous monitoring capabilities, these devices provide real-time data, empowering operators to detect and resolve issues before they escalate into serious problems.
Fuel Gas Recovery and Optimization
In a bid to enhance operational efficiency, thermal mass flowmeters are integral to flare gas recovery systems (FGRS). By monitoring and optimising the capture and reuse of gases that would otherwise be flared, these meters reduce waste and contribute to more sustainable practices. Accurate measurements enable operators to make informed decisions about energy reuse, leading to significant cost savings and increased plant efficiency.
Process Efficiency and Optimization
Finally, thermal mass flowmeters are often integrated into plant control systems, such as Distributed Control Systems (DCS). This integration provides real-time data that is essential for optimising flare operations, Minimising waste, and enhancing overall operational efficiency. By monitoring flare gas volumes, petrochemical facilities can assess energy losses and implement strategies for energy conservation and efficiency improvements.
The applications of thermal mass flowmeters in flare gas systems are extensive and vital. From ensuring environmental compliance and safety to optimising processes and enhancing energy efficiency, these devices are indispensable in the petrochemical industry. At Rocksensor, we recognize the significance of these innovations and are committed to providing solutions that help facilities operate safely, efficiently, and sustainably.
For more information email us at offers@rocksensor.in.