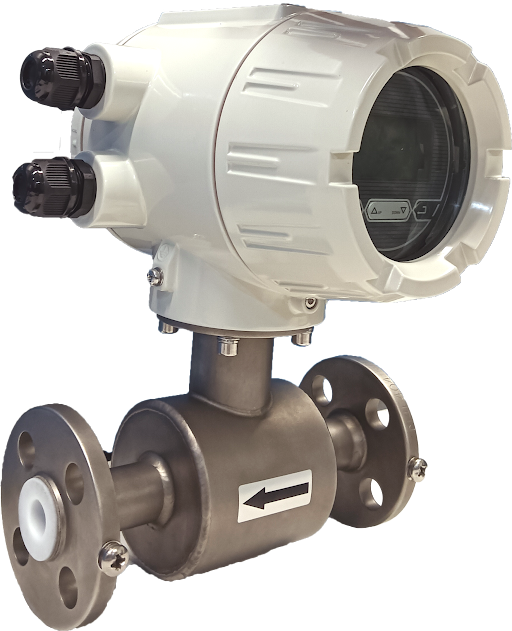
Make sure to consistently adhere to the manufacturer’s instructions for installation and upkeep to achieve optimal functioning and lifespan of the electromagnetic flowmeter.
In this blog, we will examine the critical elements involved in installing flowmeters, concentrating on three main areas: piping design, sensor placement, and machinery configuration. Proper installation is essential for ensuring precise measurements and the durability of your flowmeter system.
Installing electromagnetic flowmeters necessitates meticulous planning to guarantee accurate operation and longevity. At Rocksensor, we understand the significance of correct installation. Here are the key considerations:
1. Choosing the Installation Location
The placement of your flowmeter is vital for its effective function:
- Dry and Airy Spaces: Select a site that is both dry and well-ventilated to avoid moisture accumulation.
- Protection from Environmental Elements: For installations outdoors, employ protective covers to safeguard the meter from rain and direct sunlight.The optimal operating temperature range is from -20°C to +60°C.
- Avoiding Temperature Extremes: Keep the meter away from areas with drastic temperature changes or high thermal radiation. Insulation and proper airflow may be necessary to counteract these conditions.
- Corrosive Conditions: Avoid areas with corrosive gases. If installation in such environments is unavoidable, ensure adequate ventilation and apply anti- corrosion strategies.
- Minimizing Vibration: Install the flowmeter away from sources of strong vibrations. If the piping experiences significant movement, use fixed brackets on both sides to provide stability.
- Water Resistance: Opt for flowmeters with appropriate protection ratings — IP68 for immersion up to 3 meters, and IP65 which should not be exposed to water.
2. Minimising Electromagnetic Interference
For precise measurements, ensure:
- Distance from Electrical Equipment: Position the flowmeter at a distance from motors, transformers, and other electromagnetic interference sources. Avoid deriving power from converter distribution cabinets.
3. Ensuring Proper Pipe Configuration
Correct pipe alignment is essential for accurate flow measurement:
- Straight Pipe Length: To enhance accuracy, ensure there is at least five times the pipe diameter (5D) of straight pipe upstream and three times (3D) downstream of the sensor. This setup helps reduce flow disturbances.
4. Providing Maintenance Space
Ample space is crucial for continuous upkeep:
- Access for Maintenance: Ensure there is enough room around the flowmeter for straightforward installation and maintenance access.
5. Preventing Flow Interruptions
To facilitate seamless operation:
- Bypass and Cleaning Ports: Integrate a bypass line and cleaning ports into your installation. This feature allows the system to keep functioning even when the flowmeter requires maintenance.
6. Supporting the Flowmeter
Proper support is critical to prevent installation complications:
- Stable Installation: Avoid attaching the flowmeter to pipes prone to free vibrations. Use a stable and secure foundation for the measuring pipe.If the flowmeter is underground, make sure there are supports on both the inlet and outlet pipelines, and consider using protective metal plates above for additional safety.
Straight pipe length requirements

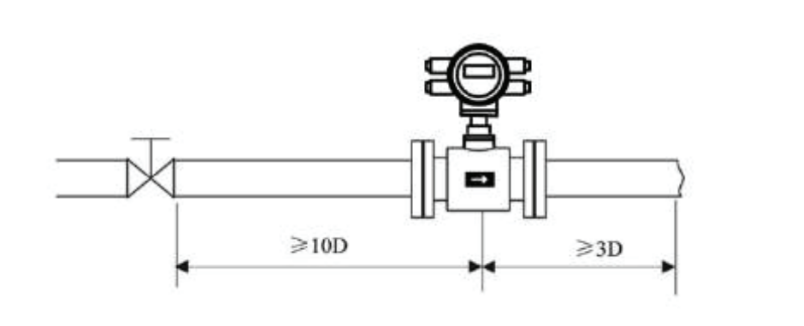
The Connection which is easy to clean pipe
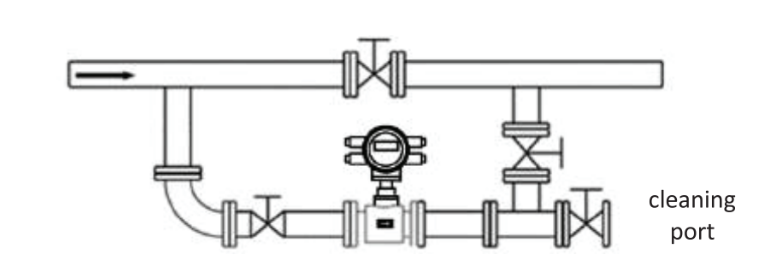
Installing Your Flowmeter: Ensuring Accurate Flow Direction Detection
When setting up your flowmeter, it is crucial to configure it correctly for reliable operation. A significant feature of this flowmeter is its capability to automatically identify the flow direction, whether it is positive or negative.
Understanding Flow Direction
The flow arrow located on the sensor housing indicates the positive flow direction as designated by the manufacturer. To achieve optimal performance, this arrow should be aligned with the actual flow in your system.
Installation Steps
- Identify the Flow Direction: Prior to installation, ascertain the direction of flow within your piping system. This step is crucial for ensuring precise measurements.
- Install the flowmeter with the arrow on the sensor housing facing the direction of the process flow. Proper alignment is key to achieving accurate flow measurements.
- Secure the Installation: After alignment, make sure that the flowmeter is firmly mounted, adhering to any additional installation guidelines provided by the manufacturer.
Preferred position for electromagnetic flowmeter installation
Installation Orientation of Electromagnetic Flowmeters
When it comes to installing electromagnetic flowmeters, the orientation is vital for ensuring precise measurements. Sensors can be set up in either a horizontal or vertical position, but each approach has particular considerations:
Horizontal Installation
For horizontal installation, it’s important that the electrodes are aligned in a horizontal plane. This arrangement helps to prevent complications caused by bubbles or sediment build-up. By ensuring that bubbles do not gather near the electrodes, you reduce the potential for zero drift and enhance the reliability of the signal coming from the converter.
Vertical Installation
In the case of vertical installations, the electrodes must also be arranged vertically. This configuration facilitates the efficient drainage of any bubbles or sediment, thereby reducing interference in measurements.
Recommended mounting position
To prevent the separation of phases in a liquid that contains solid particles or a slurry, installing an electromagnetic flowmeter in a vertical orientation is effective. This arrangement can help ensure even wear on the sensor due to the second lining, while also preventing three types of impurities from settling at the bottom of the tube and going unmeasured.
It is crucial to maintain a flow direction that goes from the bottom to the top, as this ensures that the measuring tube of the sensor remains consistently filled with the medium.
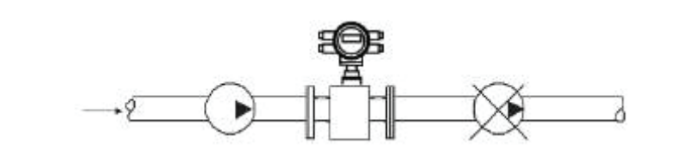
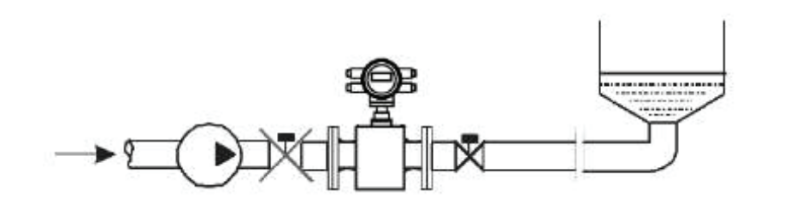
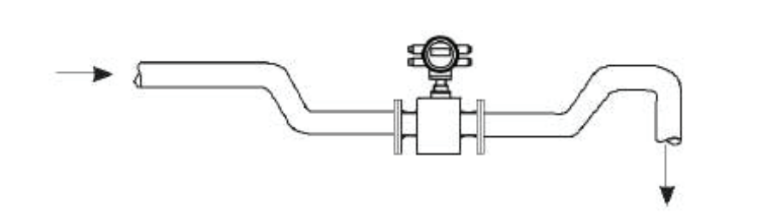
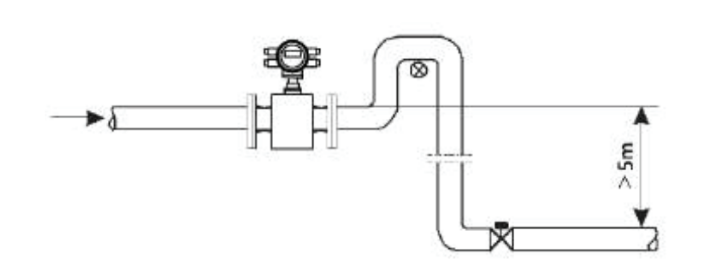
No bubbles in the pipe
The design of the piping must ensure that gas does not separate from the liquid. It is essential to install the meter before the valve since the valve lowers the pressure in the pipe, which may lead to bubble formation. Additionally, instruments should be placed in the lower section to minimise the impact of entrained air bubbles on the measurements.
Machinery Installation: Key Guidelines for Flowmeter Setup
Installing the Flowmeter Pipe
Calibration of the Pipeline: Prior to the flowmeter installation, it’s essential to calibrate the pipeline. Make sure the flowmeter’s diameter is correctly match with the user’s pipeline. For sensors with a nominal diameter smaller than 50mm, the axis deviation on the high side should be no greater than 1.5mm . For diameters ranging from 65mm to 300mm, the maximum acceptable deviation is 2mm, while for diameters of 350mm or more, it should not go beyond 4mm.
Cleaning the Pipeline: Newly installed pipes frequently have residual foreign materials, like welding debris. Before the flowmeter is set up, it is crucial to thoroughly clean out any contaminants. This step is necessary to protect the lining from damage and to prevent measurement inaccuracies that may occur from particles entering the measuring tube during operation.
By adhering to these installation guidelines, you can ensure the reliable and efficient operation of your electromagnetic flowmeter over time. For any questions, please visit our website or contact us at info@rocksensor.in We look forward to assisting you — stay connected with Rocksensor!
#Rocksensor #Flowmeter #Installlation #Transmitter #industry